Understanding Rotomolding: A Guide to the Plastic Molding Process
Rotational molding, commonly known as Rotomolding, has received
significant traction in the manufacturing business because of its
usefulness and efficiency. This process of making custom plastic
products presents a range of benefits, rendering it a chosen choice for
makers catering to industries like automotive, agriculture, medical, and
customer goods.
Usefulness in Design and Modification
One of many standout benefits of Plastics Rotomolding
is their immense style flexibility. With this particular method,
manufacturers can produce complicated forms, standard wall width, and
even double-walled structures without requiring complicated tooling.
That helps it be a perfect production selection for items like tanks,
pots, industrial equipment, and even outside furniture.
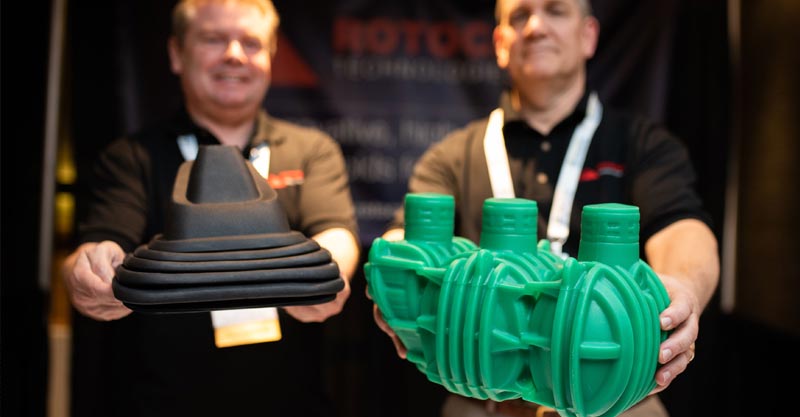
Rotomolding also enables for easy customization. Require your business brand embedded in to the product? Rotomolding can do that. Need a textured end? No problem. By having fun with shapes, manufacturers may present colors, completes, and style details that produce your product unique.
Cost-Effective for Small Generation Works
Unlike other plastic production functions like injection molding, rotomolding is more affordable for small production batches. The tooling price is somewhat lower since shapes do not need to be reinforced to handle high-pressure techniques, as observed in different creation methods. This makes rotomolding a cost-effective choice for organizations that do not need mass production.
Additionally, the slow heating and cooling pattern reduces material wastage, which will be an additional cost-saving factor. Suppliers may use different resins to accommodate the mandatory requirements, providing both freedom and effectiveness when it comes to natural substance usage.
Toughness Matches Sustainability
Rotomolding does not just produce sturdy plastic products—additionally it aligns with rising sustainability goals. Products and services created applying this method are noted for their extraordinary longevity and opposition to pressure, which explains why they are commonly useful for water tanks, traffic barriers, and heavy-duty agricultural applications.
Along with that, rotational molding employs high-grade polyethylene, which will be recyclable. It will help reduce plastic waste without limiting the structural quality of the products. Moreover, scrap substance made through the molding process may often be recycled, rendering it a wiser choice for eco-conscious manufacturers.

Consistent Quality and Efficiency
Uniformity is yet another significant good thing about rotomolding. The process eliminates the potential for weak areas usually seen in different manufacturing methods. By maintaining actually wall width and creating easy parts, rotomolding guarantees that the final product matches architectural and practical standards.
The reduced threat of defects equals a higher rate of customer satisfaction and less item returns—an essential element for makers dedicated to quality assurance.
Rotomolding stands out as a successful, economical, and environmentally conscious process for producing custom plastic products. From its versatility and modification options to its minimal spend generation method, this process continues to produce waves across industries that need advancement and durability.
Comments
Post a Comment